News, Articles & Resources
Read the latest news, updates and thoughts from our team
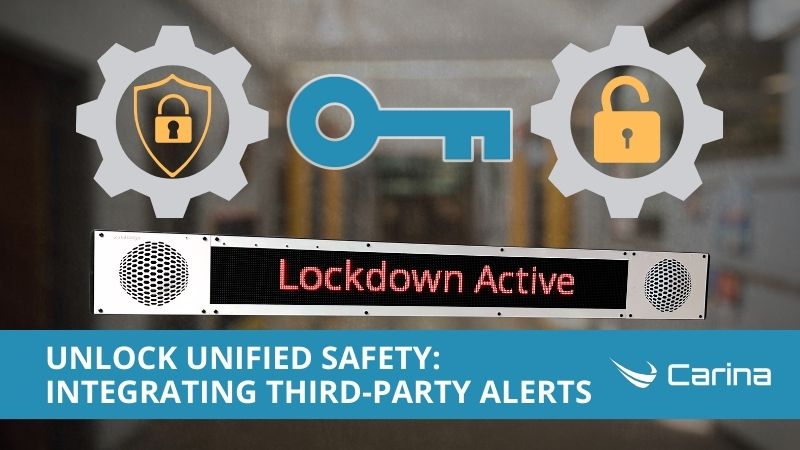
Unlock Unified Safety: Integrating Third-Party Alerts
Carina by Wahsega is a true team player, integrating with safety alert systems including Raptor Alert and 3rd party audio alert sources to enhance your school’s communication.
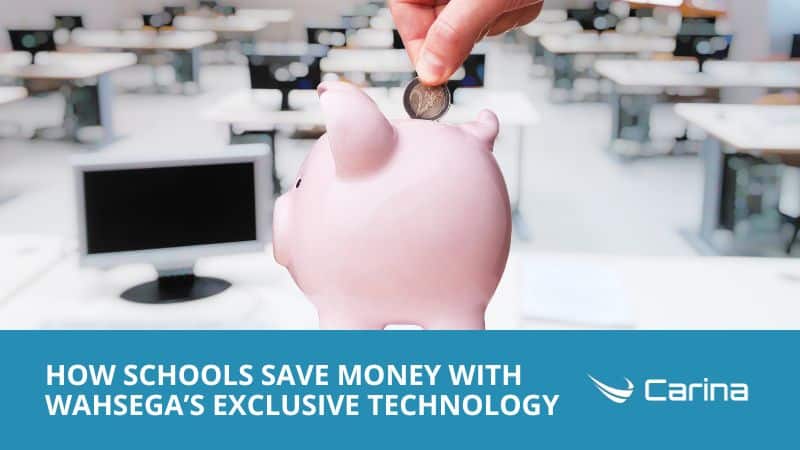
How Schools Save Money with Wahsega’s Exclusive Wiring Reduction Technology
In an era where K-12 schools are often operating on tight budgets, the need for reliable yet cost-effective technology solutions is more pressing than ever. Wahsega’s exclusive wiring reduction technology offers substantial cost savings without compromising the system’s efficiency.
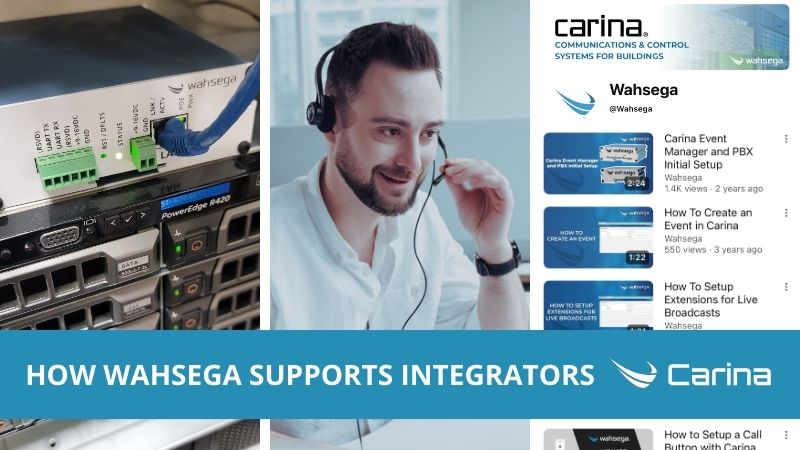
How Wahsega Supports Integrators with Training and Tech Support
Wahsega supports integrators with one-on-one training, expert tech support, and extensive online resources. Book a live setup session, troubleshoot via email support, and access video tutorials.
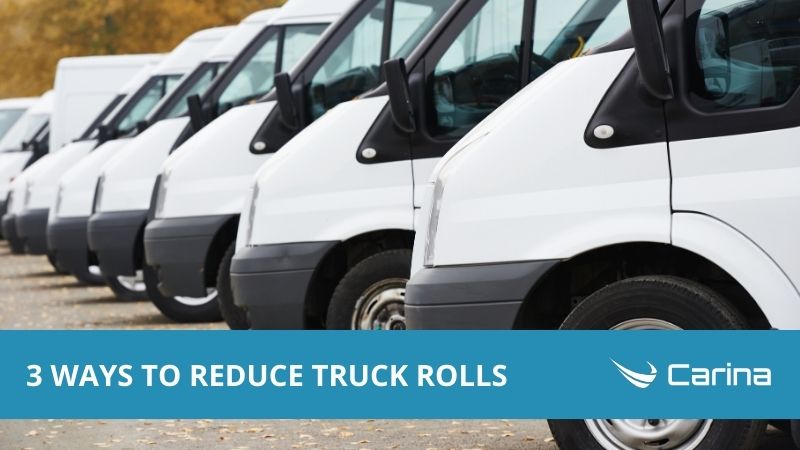
3 Ways Integrators Can Reduce Truck Rolls
Truck rolls cost time, money, and stress for both integrators and their customers. Here are three ways integrators can reduce truck rolls with Carina.
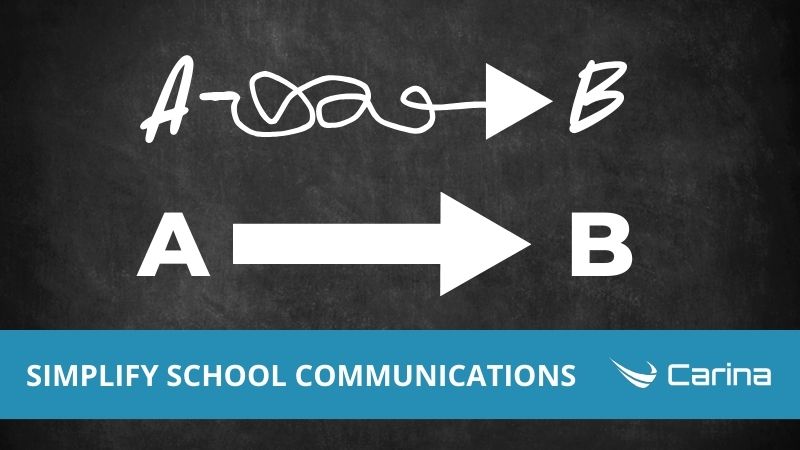
5 Ways to Simplify Your School Communications
From daily announcements to emergency alerts, ensuring clear and efficient communication is crucial for a smooth-running school environment. This article will explore 5 easy ways to simplify school communications using the Carina system.
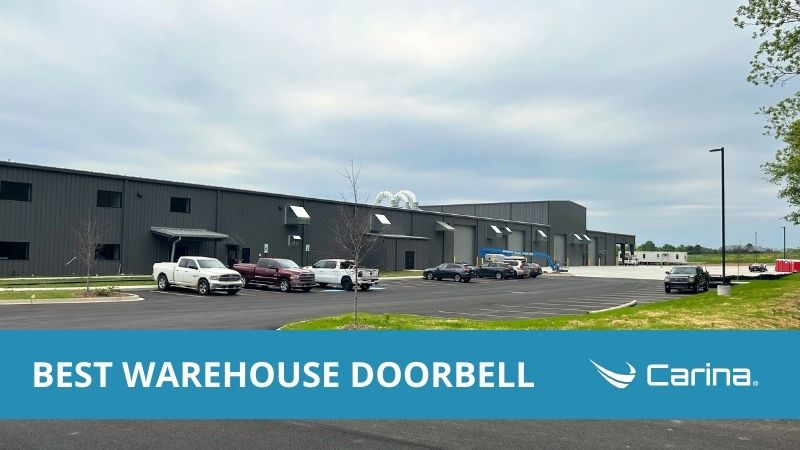
Best Warehouse Doorbell in 2025
Warehouses and manufacturing facilities heavily rely on efficient communication and safety measures, especially at loading docks where goods are received and dispatched. Among the essential components often overlooked is the doorbell system.
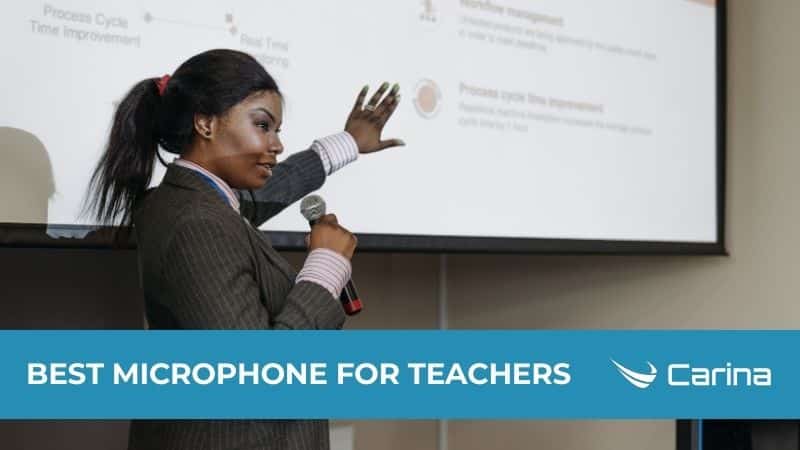
Best Microphone for Teachers in 2025
Ensuring that every student hears the teacher clearly is fundamental to effective teaching. A significant challenge in many classrooms is ensuring consistent audio coverage from the front to the back of the room.

Best Warehouse Intercom System in 2025
Investing in the best warehouse intercom system is a strategic decision that can significantly impact communication efficiency, worker safety, and overall productivity. By addressing the communication challenges faced by warehouse personnel and integrating with VoIP phones and E-stop buttons, warehouse managers can empower their teams with reliable and feature-rich communication capabilities.
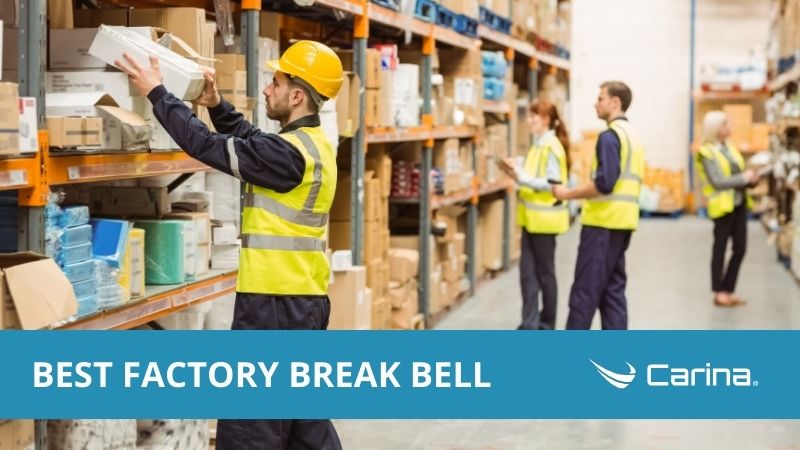
Best Factory Break Bell System in 2025
Factory break bell systems, also known as break buzzer systems or break time alarms, are crucial for coordinating the day-to-day activities in a factory. They provide structure to the working day by signaling shift changes, breaks, and emergencies, ensuring the smooth running of operations. The best factory break time bell system addresses some of the biggest problems faced by factory managers today.
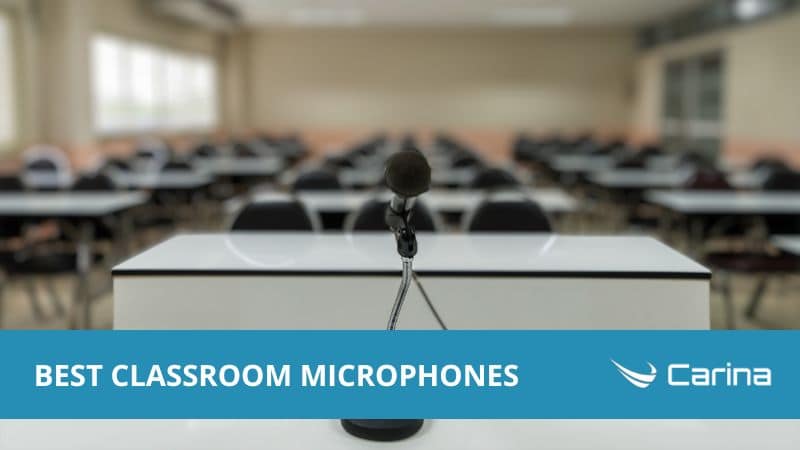
Best Microphone for Classroom Teaching in 2025
Today’s modern classroom microphone systems are far more advanced than simple legacy classroom microphone systems.
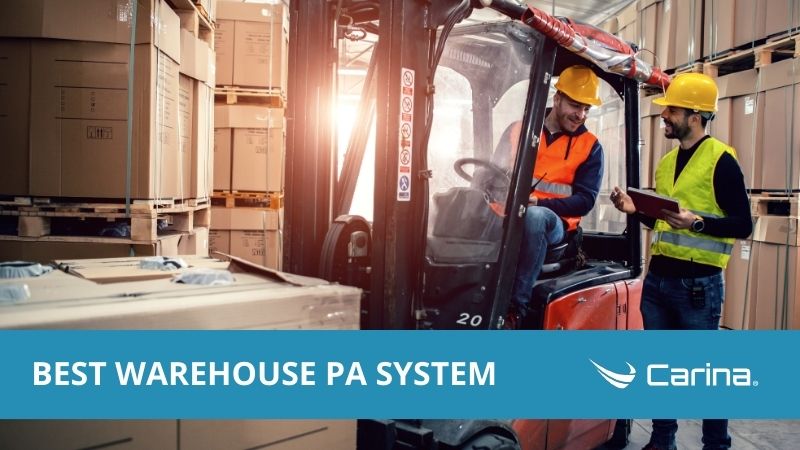
Best Warehouse PA System in 2025
In warehouses and manufacturing facilities, a major challenge is that announcements can’t be heard due to inadequate speaker volume or insufficient speaker coverage. This guide explores the key features and considerations for choosing the best PA system for your warehouse.
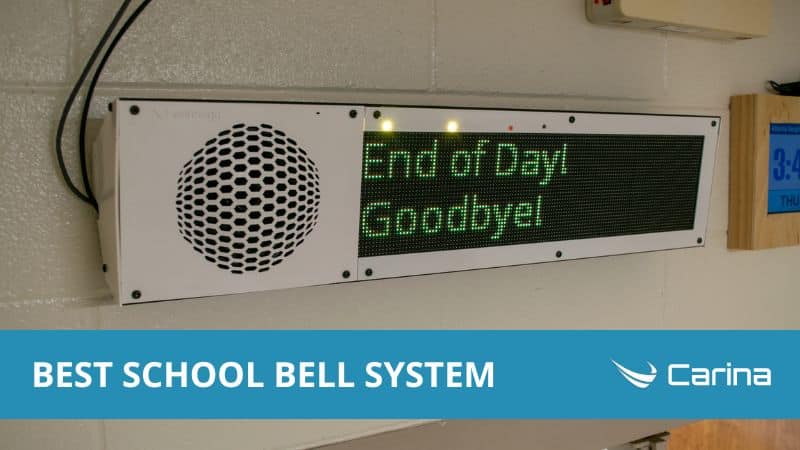
Best Bell Systems for Schools in 2025
Choosing the best school bell scheduler involves understanding your school’s unique needs, assessing system integration capabilities, ensuring customization options, and prioritizing user-friendliness. The right scheduler enhances operational efficiency, seamlessly handles schedule variations, and is an investment that significantly outweighs its initial cost.